Pictograms.
These pictograms may appear on posters, in brochures, on packaging, machines, and products.
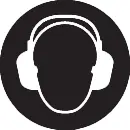
Use hearing protection.
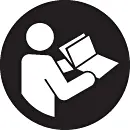
Read the operating instructions.
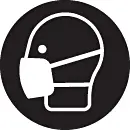
Wear a dust mask.
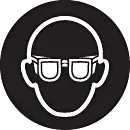
Wear safety glasses to protect eyes.
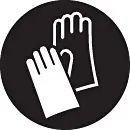
Wear safety gloves to protect the hands.
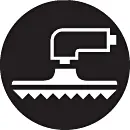
Use a back-up pad.
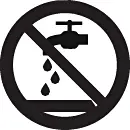
Do not use for wet grinding.
Safety Procedures by Product Type.
Belts
- Always observe safety standards as stated in ANSI Safety Code B7.7.
- Always run belts in direction of arrow printed on backing if running an overlap splice (KLINGSPOR #1, #2, or #5 splice). Butt splices (those joined with tape on the back) can be run in either direction without regard to the arrow on the backing. KLINGSPOR butt splices are types #3 and #4.
- All belts, particularly wide belts, should be preconditioned to the workplace environment. This means the belts should be removed from the original packing carton a few hours prior to use (up to 24 hours for wide belts), and hung on 4"-6" diameter pegs or bars. The conditioning rack should be located near the machines on which it is to be used.
- If bumping or ticking noise is heard while running an abrasive belt, stop the machine and check the belt or machine for damage.
- In off-hand grinding, particular attention should be paid to safety. The operator should use a firm grip, clean parts, and use caution if the object has sharp corners that might snag.
- Use extreme care if slitting or tearing belts to narrower widths, especially at the joint area.
- Only coated abrasives designed for waterproof use should be used with water coolant. Waterproof products include certain paper and cloth backings and all polyester backings.
Bonded Abrasives: Grinding Discs and Cut-off Wheels
- Always observe safety standards as stated in ANSI Safety Code B7.1.
- Do not use any bonded abrasive which has been dropped or otherwise damaged.
- Proper flanges should always be used for cut-off wheels.
- Do not over-tighten mounting nuts. Avoid “springing” the flanges.
- Inspect tools and machinery regularly for damage and excessive wear.
- The machine or tool should be as powerful as possible in order to speed up the work and to avoid stalling of drive motor.
- Steady infeed of working pressure is very important for proper cutting-off. Avoid excessive pressure, which generates heat and excessive wear.
- Avoid all side pressure to cut-off wheels.
- Bonded abrasives improperly used are DANGEROUS!!!
- Do not exceed recommended maximum speeds.
- Stand to the side when starting up bonded grinding wheels on stationary machines. Always have adequate guarding.
- Hold portable grinders down and away from operator until full operation speed is reached.
- Proper mounting of cut-off wheels and grinding discs is essential.
- Do not force a wheel onto a machine or alter the size of the arbor hole.
- Do not use a wheel which fits the arbor too loosely.
- Do not bump a grinding disc when starting to grind. Start the cut gently.
- Depressed-center grinding discs (Type 27) are best used at an angle of 15°.
Coated Abrasives: Sheets, Discs and Spiral Bands
- Pressure sensitive adhesive (PSA) discs should only be used on back-up pads or plates that are free of contamination from dirt and dust.
- If excessive glue build-up from repetitive use of PSA discs occurs, a light application of paraffin to the backing pad of plate will make the discs easier to peel off.
- All coated abrasive products should be the correct size for the machine or support pad.
- Spiral bands should not exceed specified RPMs for the rubber drums.
- Bent mandrels and damaged rubber drums should be replaced.
- When not in use, disc sanders should be placed in proper holders. Disc should not be in contact with floor or table.
- Discs should be firmly pressed onto backing pad or plate.
Fiber Discs and Mop Discs
- Proper back-up pads and retaining nuts should always be used and kept in good condition. Follow the back-up pad manufacturer’s recommendations for use.
- Use proper wrench or other necessary tools to tighten or remove retaining-nuts.
- KLINGSPOR fiber discs and mop discs should not exceed speeds of 16,000 surface feet per minute (80 meters per second).
- When grinding welds or rough edges, it is advised to grind “off” an edge, rather than “into” it.
- Place portable grinders into proper stand or holder. DO NOT place machine on its back or with disc touching table or floor.
- Do not use fiber discs or mop discs as a cut-off wheel.
Flapwheels
- Make sure that mounting plates are the proper size and are correctly fitted to the inside edge of the circular groove on the flapwheel hub. Never over-tighten fastening nuts or hub damage may result.
- Make sure flapwheel is run in correct direction of rotation.
- Observe arrow printed on flapwheel label.
- When automatically infeeding parts into a flapwheel the direction of the flapwheel rotation should be contrary to feed direction.
- Do not exceed recommended speeds on any abrasive mops.
- Use light pressure at low speeds and increased pressure at higher speeds.
General Precautions: Coated and Bonded Abrasive Usage
- Always use protective glasses and/or face shield as recommended by OSHA and ANSI Standard Z87.1.
- In some cases, it is not advisable to mix the grinding and sanding of different materials on the same machine and/or dust collection system.
- Ensure that adequate dust extraction and ventilation is maintained at all times. Avoid inhaling grinding and sanding dust. Use approved NIOSH or MSHA respirators.
- Use appropriate body protection such as leather gloves, safety shoes, and aprons.
- Inspect the abrasive product prior to usage for any nicks, cuts, tears, holes, chips, or other defects. If the product appears defective, DO NOT USE!
- If any unusual vibrations, noises, or other changes in performance occur, stop the machine and determine the cause of the problem.
- Whenever applicable, hold down workpiece using proper jigs, fixtures, and clamping devices.
- All abrasive machinery should be kept in top operating condition. Frequent checks of all moving parts such as contact wheels, spindles, idler wheels, holddown rollers, bearings, conveyors, etc., is necessary.
- Disconnect power supply before any servicing is done to abrasive machinery.
- Always allow the abrasive machinery to come to a complete stop before servicing, adjusting, or changing abrasives. Do not stop the machine using pressure to the abrasive!
- Do not exceed the recommended maximum operating speeds which are listed on products or packages.
- Do not grind near flammable atmospheres.
Proper Storage
- All abrasives, should be stored in areas which are maintained at 40% - 50% relative humidity and 60-80 degrees F (18-22 degrees C). Glue bonded coated abrasive products are especially sensitive to high humidity.
- Abrasives should be kept in their original packing containers for storage.
- Store abrasives away from a heat source, such as radiators, steam pipes, furnaces, or windows.
- Cartons should be kept away from damp or cold walls and floor where they may absorb moisture.
- Precondition abrasive belt prior to use by removing from carton and allow to adjust to ambient air, hanging on proper pegs or bars. This is especially important for wide belts, which should be removed up to 24 hours prior to use. (Also see recommendations for abrasive belts.)
- If necessary, a pre-conditioning chamber should be built to ensure constant humidity control for coated abrasives. Humidity can cause cupping of coated abrasive products, as well as premature loading and reduced product life. In belts, high humidity can cause tracking and creasing problems.
- Bonded grinding discs and cut-off wheels should be stored flat until used.
- Bonded abrasives should be handled carefully to avoid dropping or bumping. This also applies to coated abrasive flapwheels and mop discs.
- Regular stock rotation is also recommended.